Fadiga Estrutural
Diversas podem ser as causas da ocorrência de um colapso estrutural, das quais podemos citar algumas delas:
- Sobrecarga de Vento
- Corrosão
- Sobre Carga Operacional
- Sobre Carga por incrustação de material
- Sub-dimensionamento estrutural
- Fadiga
- Falha em sistemas de Proteção
- Falha no Torqueamento de Parafusos
- Projeto impropriado ao uso
- Projeto Inapropriado as condições ambientais
- Falha de Material
Segundo “Robert l. Norton” no livro “Projetos de Máquinas” a maioria das falhas em máquinas e equipamentos acontece devido a cargas dinâmicas e não a esforços estáticos e estas falhas ocorrem normalmente em níveis de tensão abaixo do limite de escoamento dos materiais utilizados.
A Fadiga passou a ser um problema observável pela engenharia com advento dos equipamentos movidos a vapor por volta de 1.800, a engenharia então passou a se deparar com falhas de materiais que suportavam com muita competência cargas estaticamente mas tinha desempenho muito ruim quando submetidos a cargas dinâmicas. Este era um fenômeno novo para engenharia então.
As Falhas por fadiga além de constituírem um custo para economia também são também objeto de estudos por envolver acidentes com perdas de vidas humanas como aconteceu na aviação.
Da Segunda Guerra mundial até hoje muito se investiu na pesquisa do assunto, visando melhorarmos os projetos, busca no desenvolvimento de novos materiais e na diagnose prematura do problema do ponto de vista da manutenção.
As falhas por fadiga iniciam-se sempre com uma pequena trinca, todos os materiais metálicos em escala microscópica nunca são totalmente homogêneos e nas regiões de concentração de tensão vão sofrer fadiga no tempo, se submetidos a cargas dinâmicas. As trincas se propagam devido as tensões de tração que ocorre no material e a taxa de propagação das trincas são pequenas por ciclo de tensão, então se a ciclagem for alta há uma tendência de falha em menor espaço de tempo.
Olhando a lista de causas de Colapso Estrutural, gostaríamos de chamar a atenção para duas das principais causas de falhas catastróficas em equipamentos sujeitos a cargas dinâmicas.
Corrosão e Fadiga são duas das principais causas de falhas em equipamento que estão em uso por um longo período de tempo.
A Corrosão então é um mecanismo muito eficiente para propagação da fadiga, qualquer peça com presença de uma trinca superficial submetida a um ambiente corrosivo, a trinca irá se propagar com maior velocidade, qualquer material submetido a tensão corrói mais rapidamente que outro que não esteja sendo tensionado. Qualquer peça submetida a tensão em meio corrosivo terá uma vida útil mais baixa. Qualquer presença de trincas vai fazer a degradação pela corrosão se propagar em mais rapidamente.
Fadiga e Corrosão esta é uma combinação explosiva do ponto de vista de surgimento de uma falha catastrófica.
Então se você encontra um equipamento submetido a cargas dinâmicas com presença de corrosão pode se um mal sinal.
Lembre-se qualquer trinca vai continuar crescendo sempre que estiver sob ação de tensões de tração cíclicas e isto vai se agravar se estiver em presença de corrosão.
A figura abaixo é um exemplo de uma falha devido a fadiga característica de uma flexão unidirecional, onde a superfície escura é da área submetida a tração onde a trina se iniciou e propagou.
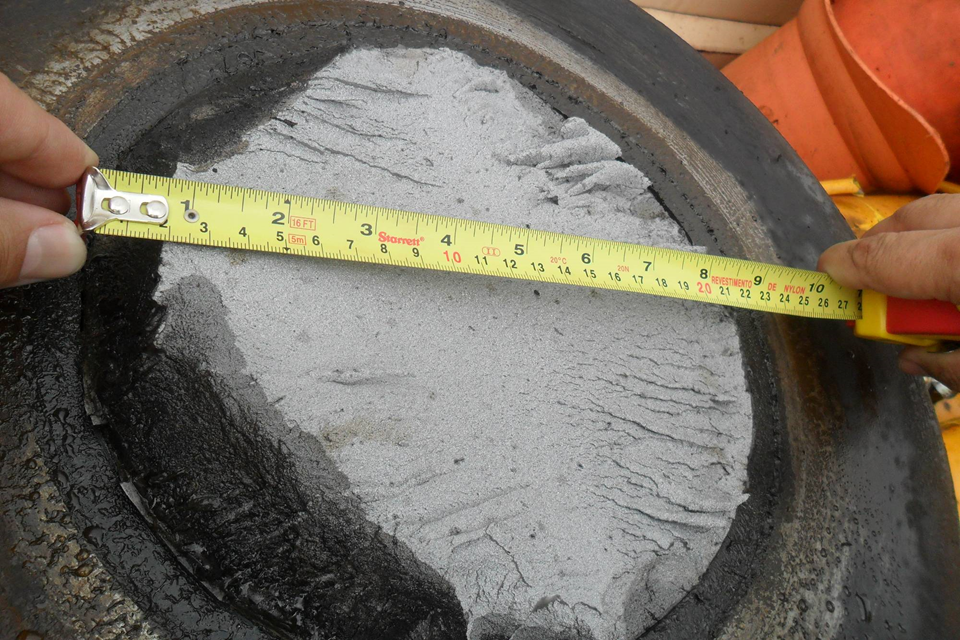
Existem três modelos de falhas por fadiga, o modelo da mecânica da fratura é o melhor modelo para modelar a propagação da trinca num processo de fadiga, é o método utilizado para predizer o tempo de vida restantes de peças trincadas.
Este método depende de ensaios não destrutivos para estimar o tamanho da trinca inicial e necessita de processamento computacional, é muito utilizado em projetos de estruturas de aeronaves.
Do ponto de vista da Segurança, Manutenção e Gestão de Risco, estabelecer programas de avaliação de componentes sujeitos a fadiga por tração e a detecção de trincas prematuramente são fundamentais e mandatórios.
Para tal são utilizados ensaios não destrutivos como; Ensaio de ultrassom, ensaio de partículas magnéticas, check trincas por liquido penetrante e check trincas por liquido penetrante fluorescente.
Os Ensaios de Ultrassom visam prioritariamente identificar trincas internas, já partículas magnéticas e uso de liquido penetrante são eficazes para detecção de trincas superficiais.
A expectativa de vida do componente informado pelo fabricante vai orientar a elaboração do programa de inspeção preditiva.
Qualquer carga de varie no tempo vai potencialmente provocar uma fadiga, em maquinas rotativas as cargas tende a ter uma amplitude constante durante o tempo, equipamentos em serviço tendem a ser submetidos a cargas variáveis, tornando mais difícil a previsão da expectativa de vida.
Recomenda-se adotar a frequência anual para ensaios não destrutivos dos componentes sujeitos a fadiga que queria controlar, esta frequência é válida para peças sem nenhum eco de defeito no ensaio de ultrassom realizados anteriormente, sem estarem submetidas a atividades em ambientes corrosivos, além da inexistência de trincas em ensaios de detecção de trincas superficiais, onde o uso de liquido penetrante fluorescente é o método mais eficaz detecção. Qualquer alteração a frequência de inspeção deve ser reduzida, pois já se caracteriza condição de início de falha.
Se você deseja saber mais ou deseja uma avaliação estrutural do seu estabelecimento, fale conosco! A Pate Antelo está pronta para atender sua necessidade!